Lúcid has started the year with many new challenges on the table. One of them is the launch of a new project where generative design and digital fabrication will take center stage.
The project, made possible thanks to the support of the CDTI, is worth 1.1 million euros and will be developed in collaboration with a renowned company in the automotive sector.
The main objective of the project is to revolutionize the bus chassis construction system, moving from welded iron profiles to carbon fiber tubes incorporating 3D printed nodes.
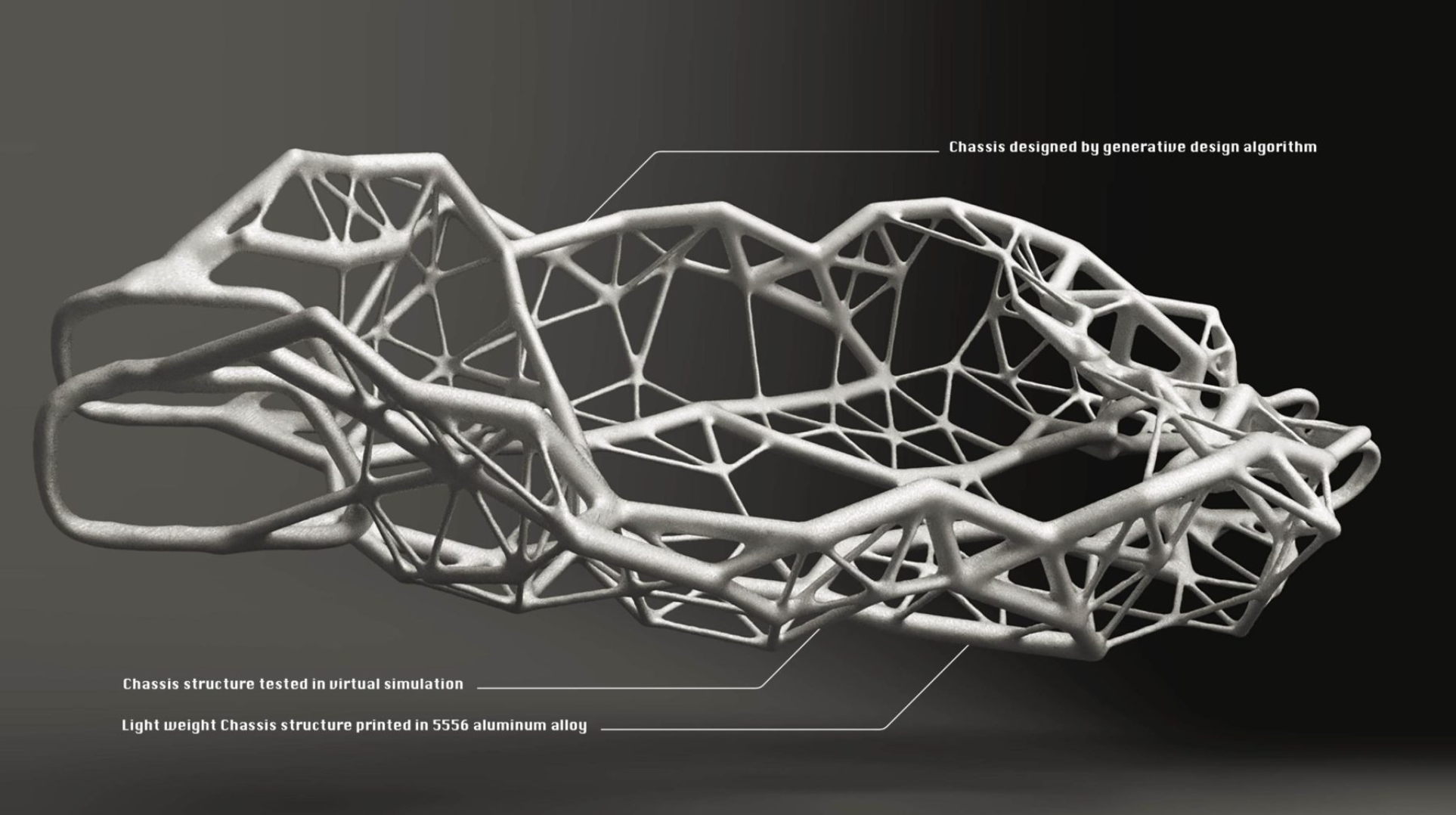
This approach would be to redefine both the manufacturing process and the bus construction system to optimize structural weight, costs and production time. The project will last 12 to 18 months and will be divided into 8 development phases to achieve all the established objectives.
The process will be developed for a renowned company in the automotive sector and will incorporate several specialized partners, including a well-known international printing company.
What is generative design and what opportunities does it offer?
Generative design allows the creation of 3D components using software that provides multiple design options, each with specific parameters. This allows the most appropriate option to be selected based on the customer's needs and aspirations.
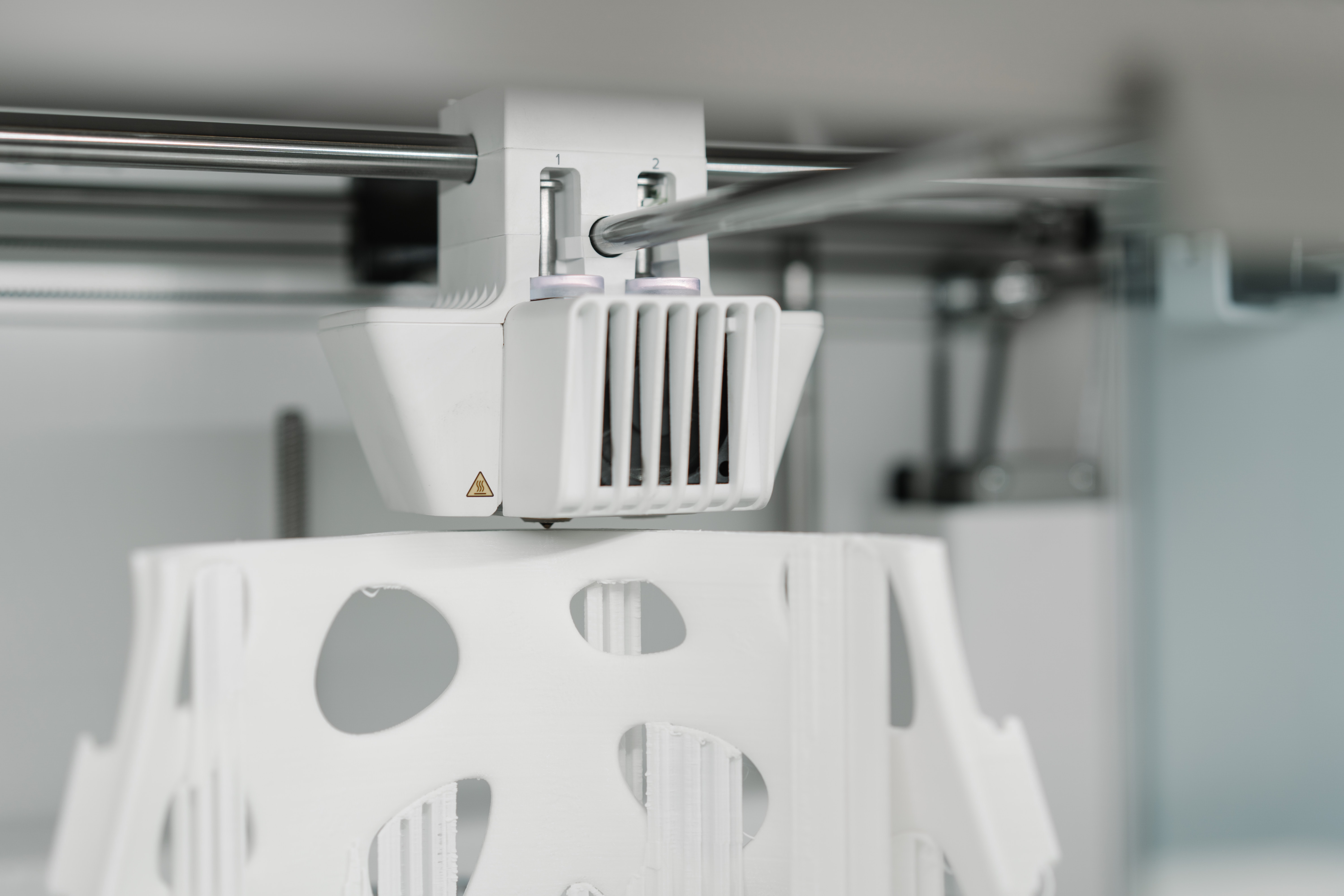
Thanks to generative design, both designers and engineers can explore different design possibilities in relation to weight, material usage and manufacturing processes. This change allows engineers to focus on design requirements rather than production constraints.
Digital fabrication: the next necessary step to optimize the design process.
In this project, Lúcid will complement generative design with digital fabrication. Digital fabrication, also known as "digital manufacturing," leverages technology to optimize the production process.
The integration of all equipment involved in manufacturing allows greater control over production, which reduces unforeseen problems, shortens lead times and improves overall productivity.
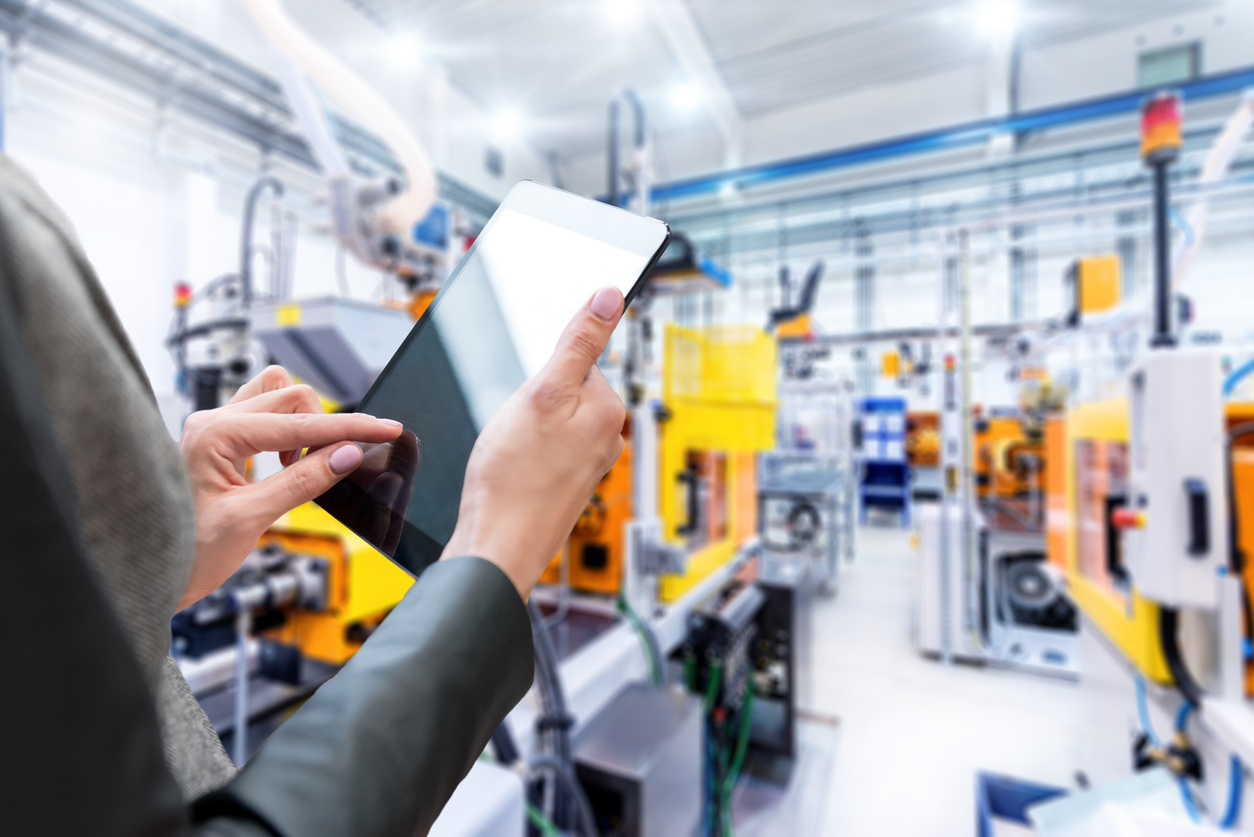
Generative design: a world of advantages for the design industry
The implementation of generative design brings numerous benefits.
Design freedom and the ability to create products from scratch allow designers to explore genuinely innovative design lines.
In addition, this technology reduces production costs by continuously optimizing materials, structures and processes, which could reduce costs by up to 50%.
In terms of sustainability, generative design promotes the use of sustainable materials while reducing product weight, enabling the creation of lighter and more innovative designs.
Generative design and digital manufacturing still have a long way to go in today's industries. There are numerous potential applications in all sectors of product design and manufacturing.
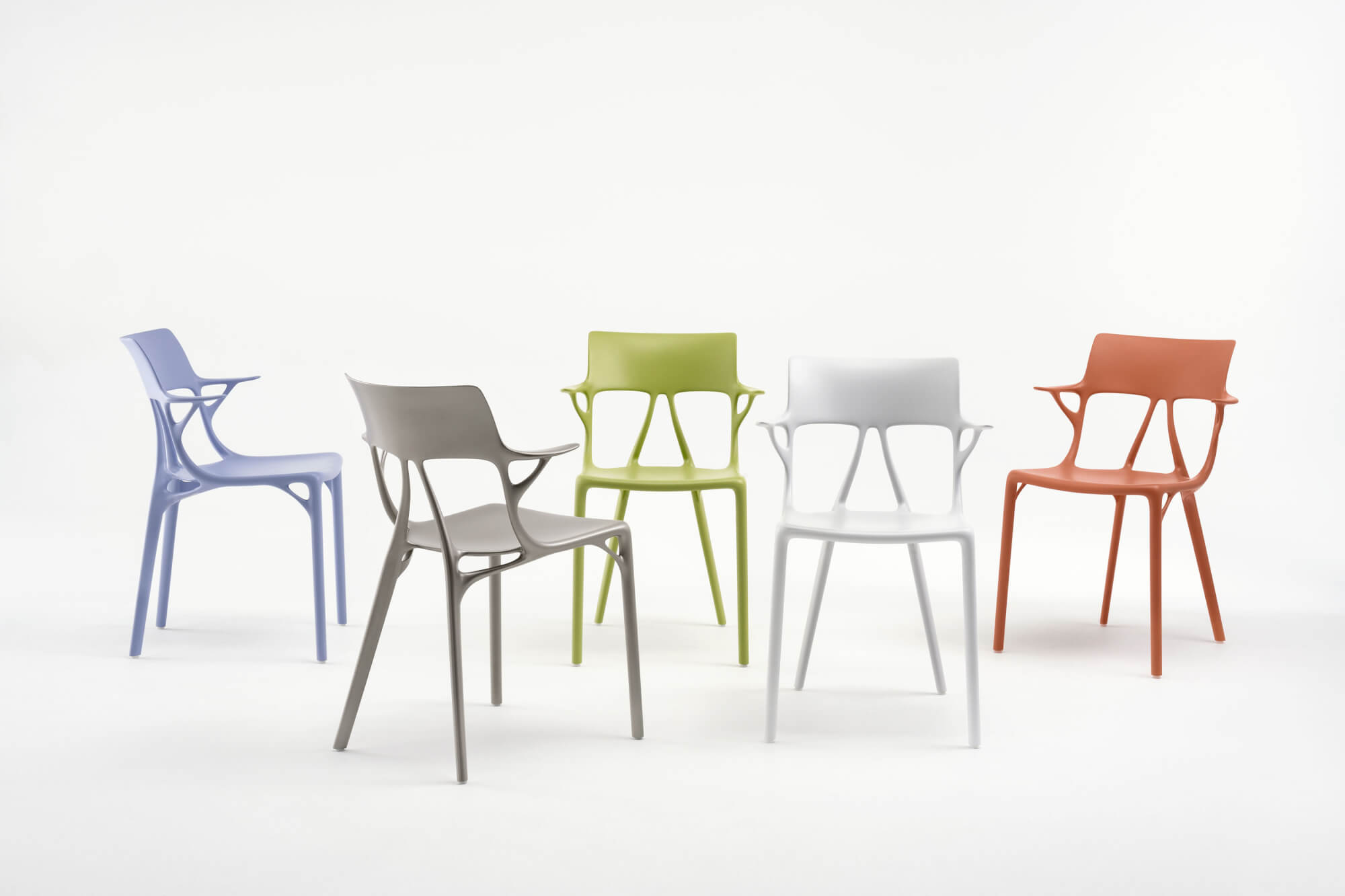
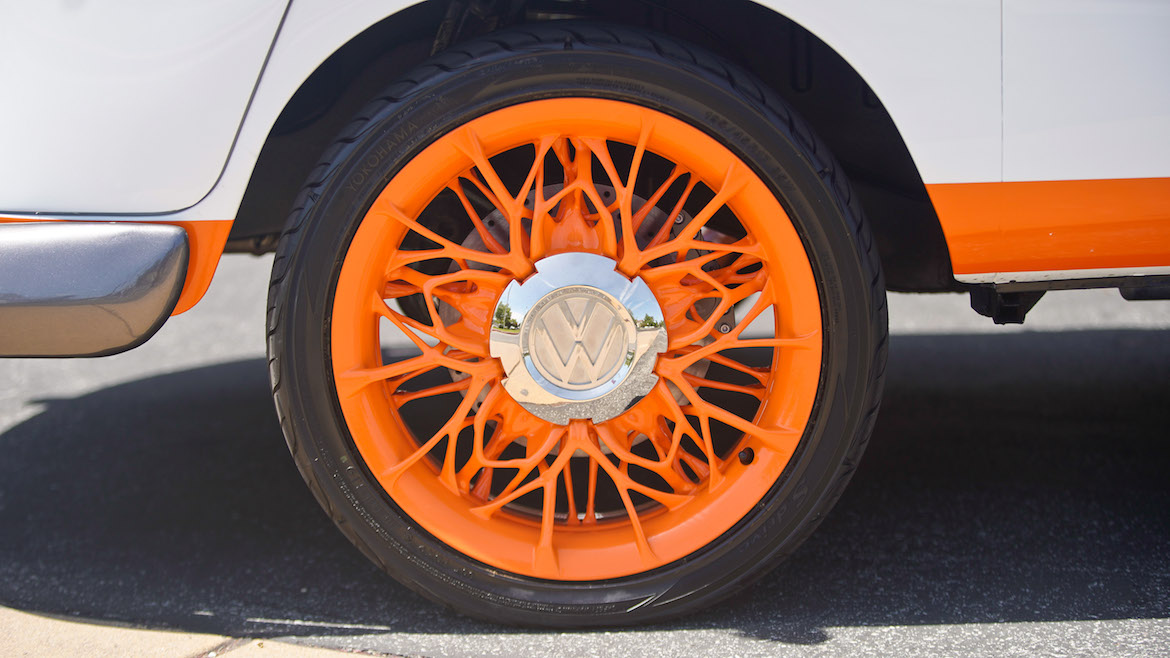
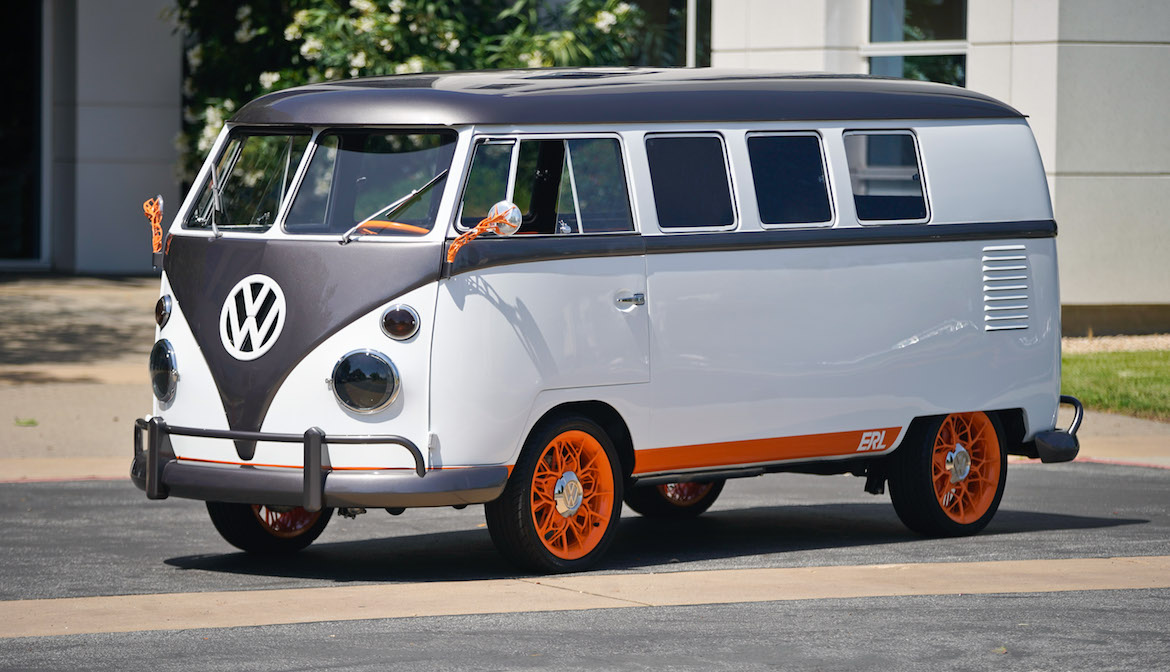
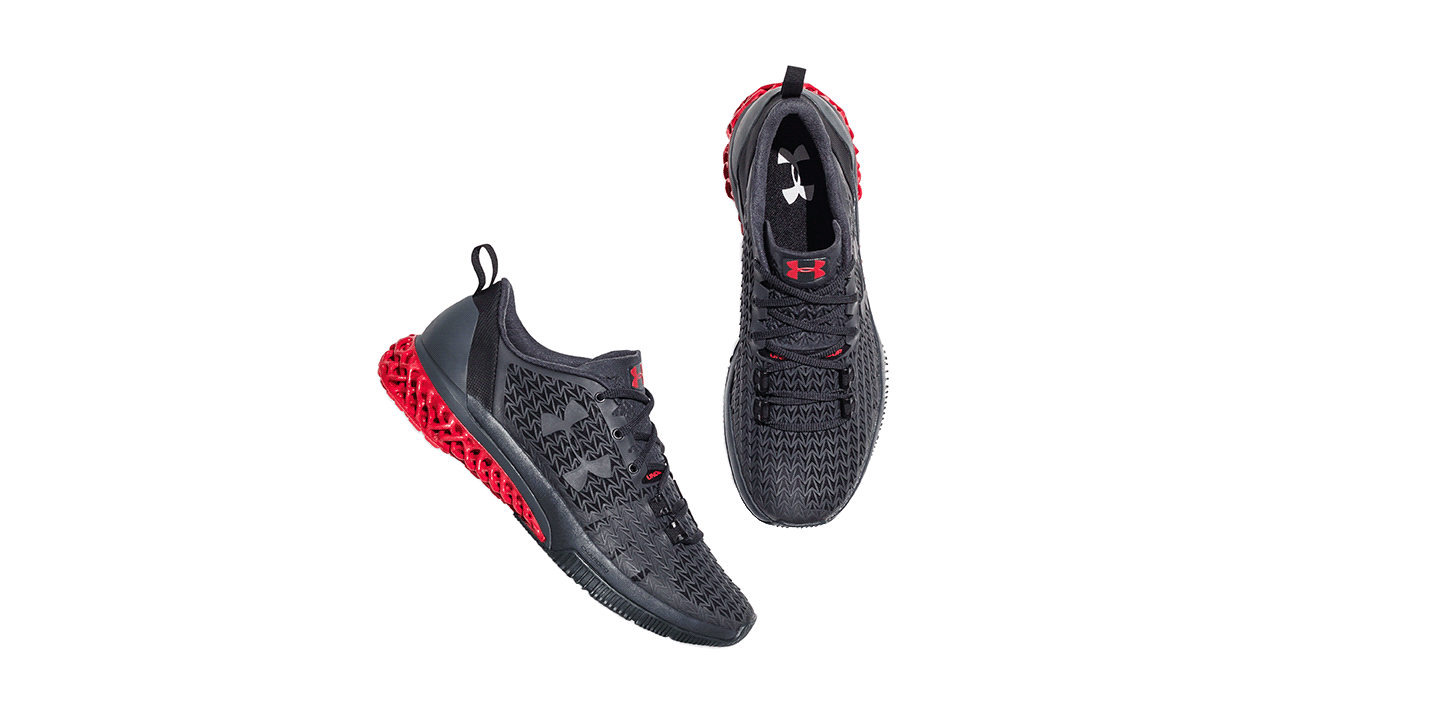