How COVID-19 highlighted the value of creativity, design and innovation
In the face of a health emergency such as the one we are experiencing, countless solutions have emerged to address new needs and mitigate the devastating effects of this pandemic on the healthcare system, the economy and people's daily lives.
A highly uncertain context has underlined the creative, innovative and collaborative capacities of our societies. We have decided to analyze this in depth so that what we are experiencing now can serve as a learning opportunity for the near future. What lessons has COVID-19 taught those of us who work in the design world?
3D printing: immediate responses to crisis contexts
Many of the solutions that have emerged in recent weeks have been developed thanks to 3D printing. This technology has proven to be a viable option for designing and mass producing products with immediacy and at a very low cost. It is an ideal alternative to respond to crisis situations that require quick and effective solutions.
Examples include face shields designed for healthcare workers and the production of ventilator valves. These alternatives aim to complement limited traditional resources by offering viable, scalable, cost-effective and fast production solutions.
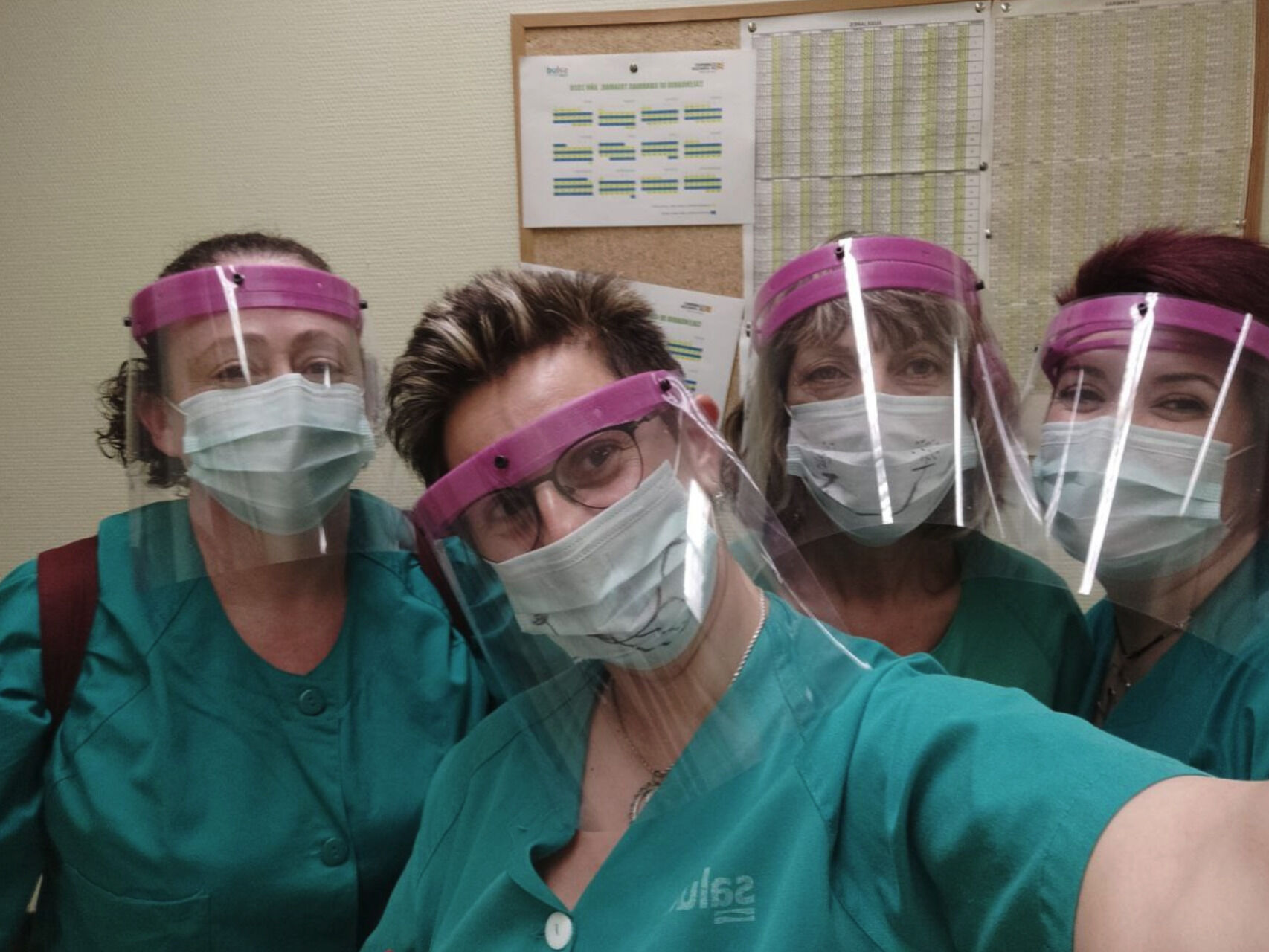
Another example is the field ventilator. designed by El Consorci de la Zona Franca de Barcelona (CZFB), Leitat, Consorci Sanitari de Terrassa and Hospital Parc Taulí de Sabadell, in collaboration with several companies. They have developed the first industrializable mechanical field ventilator manufactured by 3D printing. This means that it has a scalable production capacity.
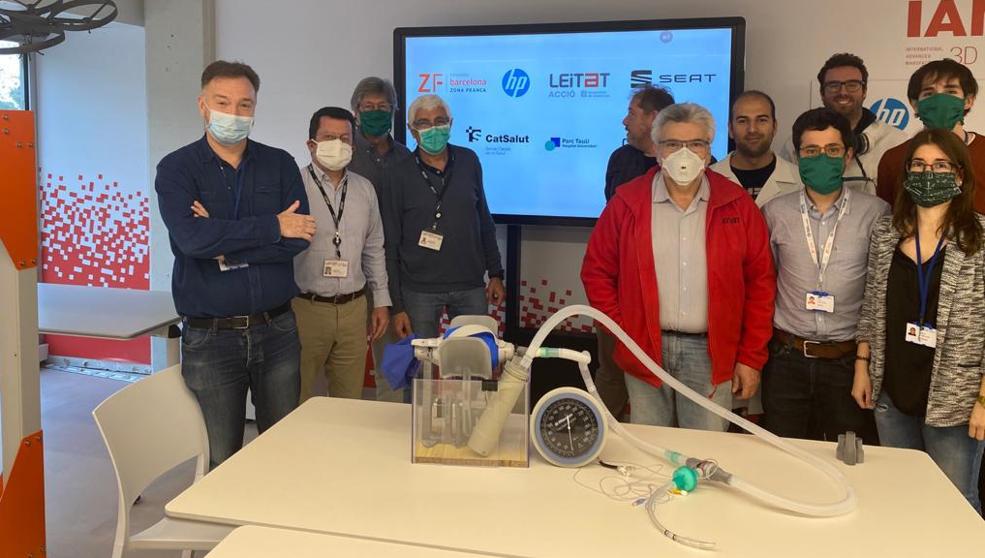
Reuse of products to meet new needs
While human innovation has no limits, in a crisis, solutions can be surprisingly creative and do not always have to start from scratch; sometimes, it is enough to reuse an existing product.
One example is the work done by SEAT, which used windshield wiper motors, factory-printed gears and gearbox shafts to design a new emergency ventilator now used in hospitals.
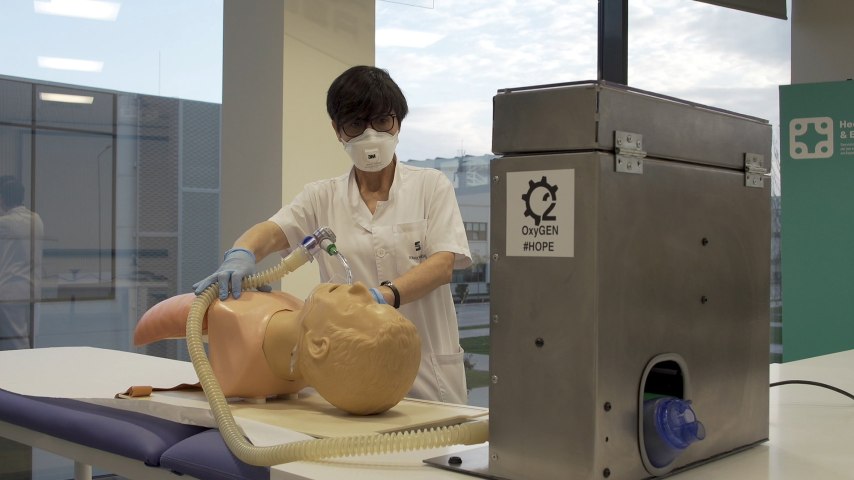
The value of do-it-yourself
In crisis situations where resources are scarce, it is crucial to combine efforts to achieve solutions as quickly as possible. This is where the Do It Yourself (DIY) movement becomes valuable. Many healthcare workers and people at risk are in need of essential protective equipment, and any contribution, even on an individual level, helps to alleviate the crisis.
In recent days, numerous tutorials have emerged on how to make masks that protect against COVID-19. Online, you can download instructions for printing face shields with a 3D printer, among many other alternatives.
These initiatives help to increase the volume of solutions available at a time of great need.
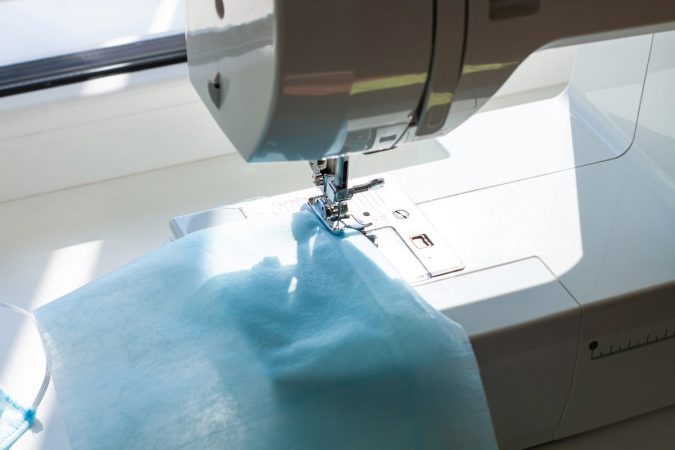
More sustainable designs than ever before
As we mentioned in our last post on designing for the circular economy, a sustainable design follows three principles: it must be made of recyclable materials, have remarkable durability, and be easy to repair or reuse. One of the effects of this crisis is that the scarcity of resources has pushed us to adopt such designs.
This is what happened with the well-known Decathlon snorkel masks, originally designed for recreational use, which have been repurposed as high-flow oxygen masks.
Unlimited collaboration
If there is one thing the COVID crisis has taught us, it is the power of collaboration in society. In fact, many of the solutions that have emerged recently would not have been possible without the selfless teamwork of various stakeholders. Numerous online platforms have been created to connect the various stakeholders in the design process.
One example is the Coronavirus Makers project, which aims to develop open source plans and instructions so that anyone with a 3D printer can participate. According to reports, there are now more than 10,000 makers coordinated through Telegram, creating masks, face shields, fans and protective booths in record time.